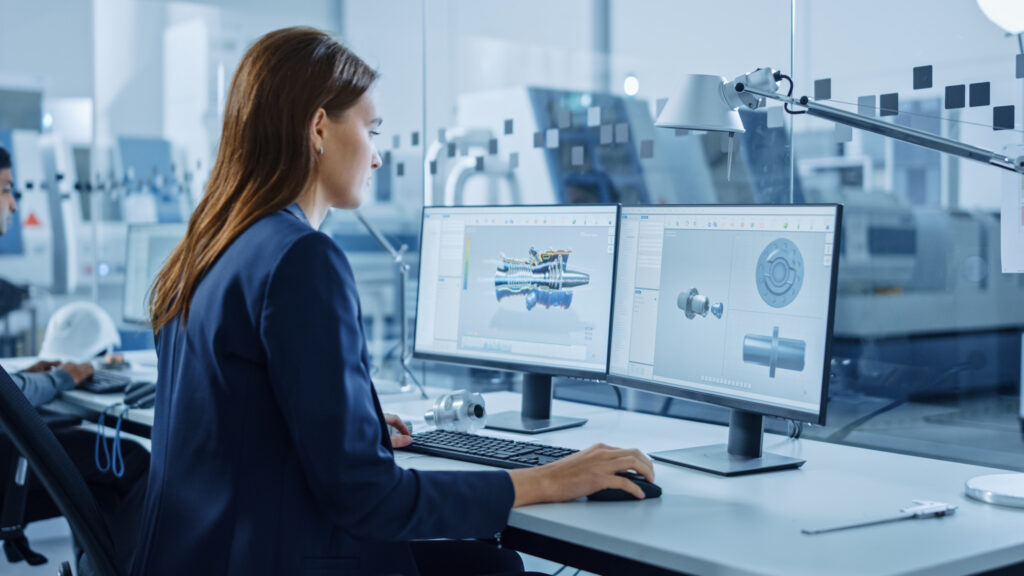
3D printing technology
Over the past few decades, 3D printing technology has undergone a remarkable evolution, transforming from a niche prototyping tool into a mainstream manufacturing method with widespread applications across industries. In this blog post, we’ll explore the journey of 3D printing, tracing its evolution from its origins in rapid prototyping to its current role as a versatile and viable production technology.
1. Rapid Prototyping Revolution: 3D printing first gained prominence in the 1980s as a revolutionary prototyping tool, offering designers and engineers a faster, more cost-effective alternative to traditional prototyping methods. By building layer upon layer of material from digital designs, 3D printers enabled rapid iteration and refinement of prototypes, accelerating the product development cycle and reducing time-to-market for new innovations.
2. Expansion into End-Use Production: As 3D printing technology matured and materials improved, its capabilities expanded beyond prototyping into end-use production applications. Today, 3D printing is utilised in a wide range of industries, including aerospace, automotive, healthcare, and consumer goods, to manufacture final products with complex geometries, lightweight structures, and customised features that are difficult or impossible to achieve using traditional manufacturing methods.
3. Advancements in Materials and Processes: One of the key drivers of 3D printing’s evolution has been advancements in materials and processes. From plastics and resins to metals, ceramics, and composites, the range of materials compatible with 3D printing has expanded significantly, enabling manufacturers to produce parts with diverse properties and performance characteristics. Additionally, innovations in printing technologies, such as selective laser sintering (SLS), stereolithography (SLA), and binder jetting, have unlocked new possibilities for high-resolution, high-speed, and multi-material printing, further fueling the adoption of 3D printing for production applications.
4. Integration into Traditional Manufacturing Workflows: Another significant development in the evolution of 3D printing is its integration into traditional manufacturing workflows. Rather than replacing conventional methods outright, 3D printing is increasingly being used alongside traditional manufacturing processes like injection moulding, casting, and machining to complement and enhance production capabilities. This hybrid approach, known as additive manufacturing, combines the strengths of both subtractive and additive techniques to optimise efficiency, reduce waste, and unlock new design possibilities.
In conclusion, the evolution of 3D printing technology from prototyping to production represents a paradigm shift in the manufacturing landscape, offering unprecedented opportunities for innovation, customisation, and efficiency. As 3D printing technology continues to advance and mature, its impact on industries ranging from aerospace and automotive to healthcare and consumer goods will only continue to grow, reshaping the way products are designed, manufactured, and brought to market. Whether it’s producing complex prototypes, bespoke components, or end-use products on demand, 3D printing has emerged as a transformative force that is revolutionising the future of manufacturing.
Are you looking for advice on 3D printing or printing equipment? Get in touch with us today to discuss your needs.